Considering a new TIG welder? Before you part with your hard earned, there are important and key points to know first.
- Transformer or Inverter
Until 2005 Tig Welder transformer machines were very common in the new machine market and due to their limitations in control and weight have been replaced by modern inverter welder products. Transformer machines would step down the primary input, either 240V single phase or 415V 2 / 3 phase to a lower voltage welding current. The output of the transformer would then either be rectified for DC welding or in the case of an AC tig welder the machine would then step the output to create a square wave like output. The devices used for creating the stepped output were triacs. Generally pulse weld output and frequency control were not achievable in affordable units so the control panels are relatively simple. Your budget will address this one as transformer machines are mostly found in the second hand resale market.
Inverter machines despite their complex build are relatively simple in design. The incoming supply is rectified into DC. The DC current is inverted to AC by way of a full or half bridge inverter circuit at high frequency and then the AC is stepped down via a transformer. The output of the transformer is rectified into DC and this current is used in straight or alternating reverse polarity by a second stage transistor array. What are the benefits of an inverter machine? Read on.
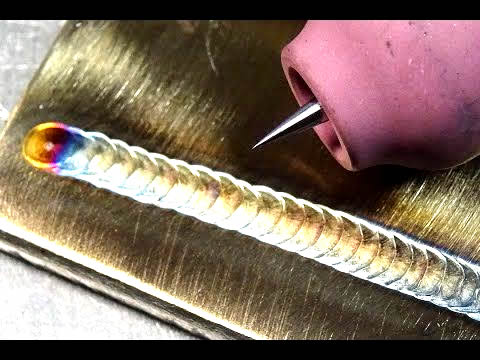
Precise arc control with an inverter tig welder
2. What are the benefits of an inverter welder?
Due to the high frequency used to create the inverted AC wave in the step down transformer, magnetic flux is reduced and as a result the transformer shrinks in size and weight. When comparing a 50 Hz 200 amp transformer from an old transformer machine to a 100Khz 200 amp transformer from an inverter machine the difference can be 80:1, that is 80 kilograms to 1 kilogram. This is all to do with the operating frequency of the step down transformer.
So weight is the first key benefit, next is control. Modern inverter machines control the inversion of the AC before the step down transformer so they can also pulse the current. This type of product is called a pulse welder.
3. Do I need a pulse Tig welder?
Pulse welder mode is a beneficial feature that can assist the operator in lowering the overall weld current by pulsing it. When a pulse completes there is a period of time when the base current is introduced and it is lower, generally by 30%, than that of the pulse. This pulse base cycle allows the material to melt and solidify and achieve a level of melt that prevent excess or runaway heat so is an ideal process for thin walled material, and whilst we are on the subject of material….
4. What material can be welded with a TIG?
A TIG welder machine can weld any material. Think of the TIG as an electron beam heat pump with electrons flowing from negative to positive electrodes. When you add heat to a metal and enclose it in an inert gas shield that metal will melt. All metals are TIG welded with a negative TIG torch electrode except aluminium or it’s alloys which requires an alternating current. Aluminium is covered with an oxide layer that melts at 3 times it’s temperature so when using an AC waveform the oxide is removed from the surface when the TIG torch is charged positively and the aluminium work piece melts when the TIG torch is charged negatively. If you don’t plan to weld aluminium then a straight DC welding machine is suitable. If on the other hand you plan to weld all materials then your only option is to invest in an AC/DC TIG. Machines with ACDC welding wave forms are more expensive as they contain a second stage transistor array for switching the output current in either straight or toggling reverse polarity, DC or AC.
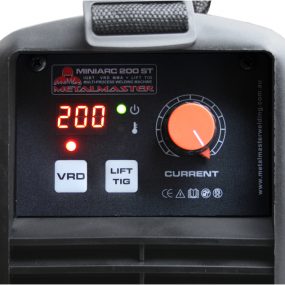
Tig welding control with a single knob
5. How many controls are required to weld?
Only one control is required and that is amperage , the other controls just make things easier. For AC welding having a balance control is a must and a frequency control for the AC waveform is icing on the cake. Consider the type of welds you will be creating and there is no harm in getting a very complicated product. Just because a feature is there doesn’t mean it needs to be used but as you grow into a product and gain experience you will find more adjustment can be introduced to your welds by using these extra features.
6. Multi process or Multi Function or single function?
If you buy a multi function welding machine, you can do several things such as MIG and TIG or TIG weld and Plasma Cut. It is an advantage to buy a multi function welder every time and here is why.
When it comes to inverter based machines they already have an inverter circuit creating welding power. This welding power is available in either constant voltage (CV) or constant current (CC). A CV machine like an inverter MIG can also be CC machine like a stick or TIG welder simply by switching what it is controlling, that is instead of being a MIG and controlling arc voltage, it starts to control arc current and works as a Stick welder. With plasma cutters it is the same process but they operate at a higher voltage around 100 volts DC under load so they have a second transformer winding and changeover relay to switch the plasma current from the step down transformer to the output. Metalmaster welding machines have a 5 year warranty regardless of whether they are single function or multi function welding products. The only time you would specifically stick to a single function product is when it is located in a fabrication shop and it is being used for one purpose most of the time, in such cases staff sharing the different functions is counter intuitive to productive work places in order to just to save a few bucks.
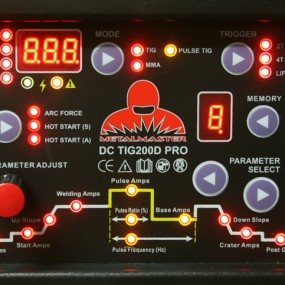
Digital Tig Welder Control Panel
7. Do I need a digital panel or are analogue knobs ok?
Analogue panels are fine and have plenty of control. The Metalmaster analogue panel machines still have a digital main board with microprocessor control but employ analogue to digital converts which allow the operator to still experience old world charm on a modern machine.
If on the other hand you want every possible feature available then a digital panel allows for maximum features in the smallest space. Digital welders also have memory functions that allow the saving of preferred parameters and are ideal in fabrication shops where jobs can be stored and recalled at the press of a button.
8. How many amps will I need?
TIG welder penetration is all about amperage with a rough guide being 30 amps per mm of material thickness in aluminium and 25 amps per millimetre in steel. These figures are for full penetration into the material and don’t take into account weld joint type, ambient temperature or mass of material being welded. For a 200 amp machine you will easily weld 8mm plate from one side and if you want to go really thick you can pre heat with LPG or propane in order to raise the surrounding weld area by a few hundred degrees. Another technique for pre heating is to run the torch up and down the weld zone for a few minutes before starting the weld itself.
9. Tig Welder Duty Cycles, what are they and do they matter?
A duty cycle is the rating the manufacturer gives a welding machine so that the operator has a clear idea of how useful the machine is for welding at high amps or for prolonged periods. The duty cycle of an inverter welder is given as a percentage of time in a 10 minute period that the machine can output the set current at an ambient air temperature of 40 degrees celsius.
For example there are cheap 200 amp welders that quote a duty cycle of 20% at 180 amps, this would indicate very poor performance at 180 amps and even worse at 200 amps. To the contrary, Metalmaster ACDC TIG welder products have a rated duty cycle of 60% at 200 Amps making them ideal for dependable use and for prolonged periods of time.
10. What to expect with a long welder warranty.
Warranty on welding machinery varies between manufacturers with most being between 1 and 3 years. It is critical to read the fine print of any warranty as some only warrant control boards for 1 year whilst covering a transformer (which will never fail) for 3 years. All Metalmaster welding machines come with a 5 year warranty for parts and labour giving the original owner many years of peace of mind.
You can further read about our range of DC Tig welders here or see our AC/DC Tig range here.