Perhaps one of the most widely adopted processes, TIG welding is used for fusing of both ferrous and non ferrous metals. The TIG process can be applied to all kinds of areas in commercial industrial manufacturing and is a valuable skill to possess whether you are a beginner or seasoned veteran.
Before you make a start in the field of TIG welding, a thorough understanding is required as to the type of waveform that will be applied to the current based on the material being welded. Although the most modern welding rigs feature multiple AC waveforms, the fundamentals to weld any metal are in the current being applied to the welding arc, at it’s most basic level you will need to use either alternating current square wave (AC) or direct current (DC).
An AC Current or DC : What is the Difference When Applied to TIG Welding?
For anyone looking for an explanation of these terms you have found the right place, on a TIG welding machine the AC or DC setting sets the direction of current flow in a conductor which is chosen based on the parent material being welded. Interestingly this is in the opposite direction of the electron flow. Whilst electrons are negatively charged and flow from negative terminal to positive terminal, the current flows from positive terminal to negative terminal.
A DC current is a constant flow in one direction, in a DC welding process the current can change it’s intensity referred to as amperage but it will not change it’s direction. A DC current is used when welding all metals except those that oxidise such as aluminium.
An AC current alternates it’s direction continuously, in an AC welding process the current can change it’s period of direction known as frequency, it can change it’s ratio of direction known as balance and also change it’s amplitude referred to as amperage. AC current is used for aluminium and it’s alloys. When electrons flow from the workpiece to the positively charged tungsten during the cleaning half cycle, they remove the oxide layer from the surface of the aluminium by blowing it off from beneath and the gas shield of inert argon prevents new oxide forming thus allowing the molten pool of pure aluminium to fuse.
AC Frequency
Diagram showing the effect of AC Tig welding frequency adjustment
AC Balance
AC balance is used to control the amount of cleaning known as oxide removal whilst welding aluminium and it’s alloys. More cleaning, that is more bias of electron flow toward the tungsten does increase oxide removal, the heat is also directed toward the tungsten and it melts forming a ball due to surface tension of the molten tungsten. Less cleaning allows more penetration toward the workpiece. A sweet spot can be found between 20% and 40% of AC balance toward the positive half cycle.
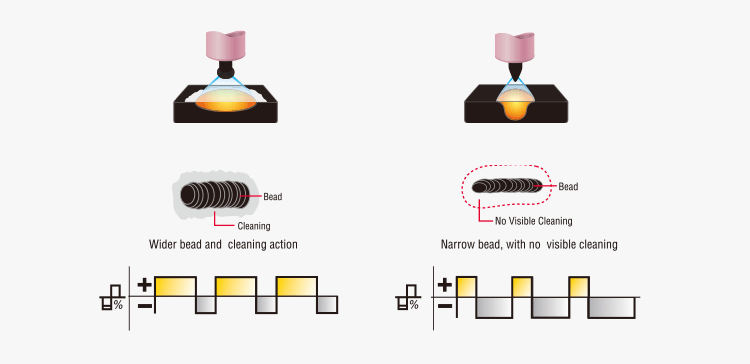
Welding Aluminium with DC, it’s not a magic trick.
You may have heard or have experienced welding aluminium with your MIG welder and it is only a DC current welding machine. What is this black magic you may ask? It’s not magic and can be understood in the previous section detailing AC balance for TIG welding.
In a MIG welding machine, when the electrode is charged positively, the electrons flow toward it and blow away the oxide layer from the workpiece. In this situation it is cleaning action ramped up to 100% as there is no negative half cycle reversal. The electrode is disintegrated instantly due to the massive amount of heat forming on it. It sounds ominous for the electrode however in the case of a MIG welder, the electrode is the wire and as the electrode is melting it keeps getting replenished so never burns out. The molten electrode droplets are bombarded into the workpiece by the immense magnetic fields generated in the welding arc. Only in this situation is it possible to effectively weld aluminium with DC.
AC DC TIG Pros
Good penetration
Neat weld appeal
Ability to control heat and filler easily
AC DC TIG Cons
Slower than MIG
Not as effective as MIG in repairing salt exposed dingy hulls